Join us in advancing geotechnical engineering. Email: una@kellegco.com
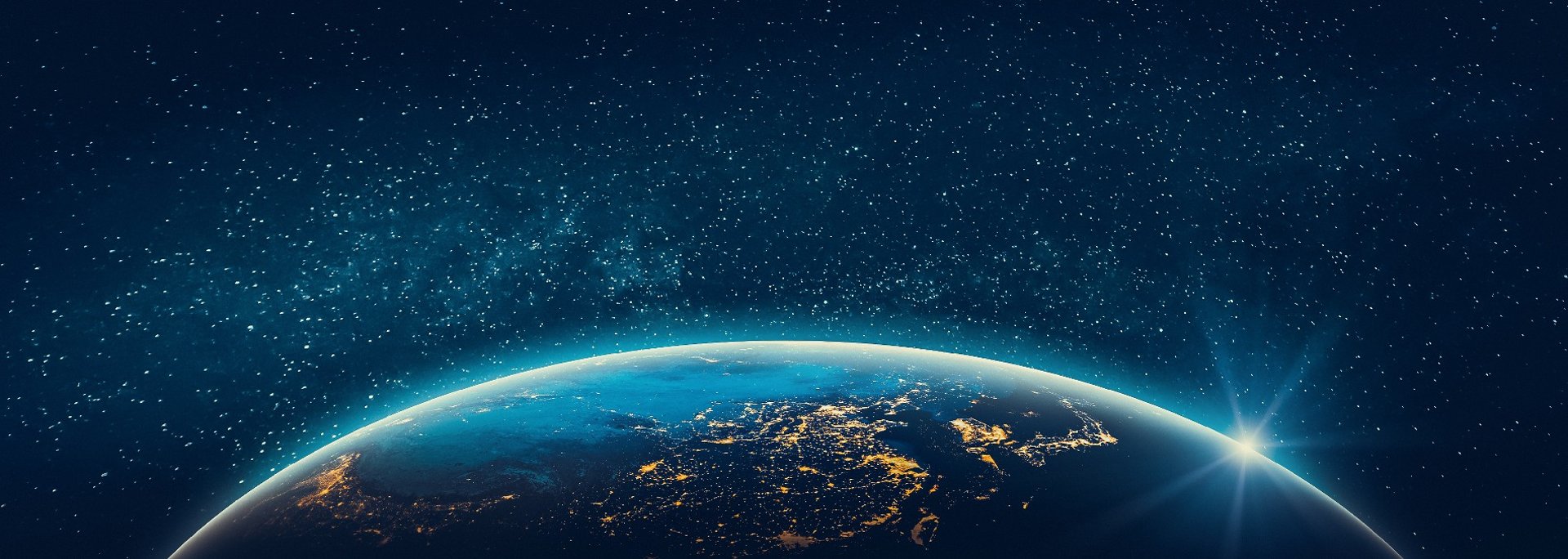
Anti-Corrosion Technology for Drill Rods Used in Hydraulic Rock Drill Jumbo
The corrosion resistance of the drill rod has become a key factor restricting its service life and performance.
Una
9/11/2024
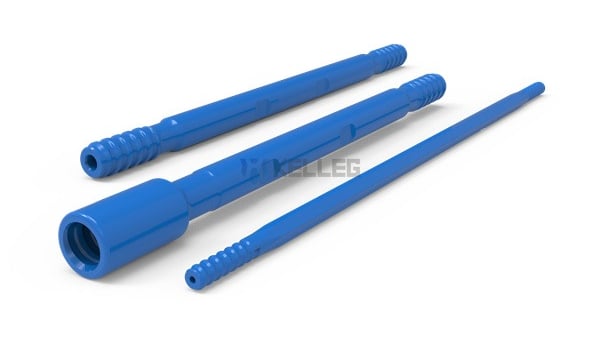
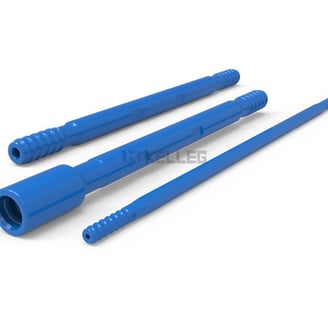
In modern industry and construction, hydraulic rock drill jumbos have become indispensable equipment with high efficiency and precise performance. As the core component of the drill jumbo, the quality and performance of the drill rod are directly related to the efficiency and results of the entire rock drilling operation. However, in the face of harsh working environments, such as humid mines, highly corrosive mine water, and sea breeze erosion during long-distance shipping, the corrosion resistance of the drill rod has become a key factor restricting its service life and performance.
The importance of drill rod corrosion protection
In the work, the drill rod is in direct contact with the rock and withstands huge impact and friction. At the same time, the salt and chemicals in the mine water, as well as the moisture and corrosive gases in the air, will corrode the surface of the drill rod, causing its performance to deteriorate or even early scrapping. It not only increases the operating costs of the enterprise but may also hinder the progress of the project and affect the smooth progress of the overall project. Therefore, effective anti-corrosion treatment of the drill rod for hydraulic rock drill jumbos is essential to enhance the tool's longevity and maintain work efficiency.
Introduction to phosphating wax dipping anti-corrosion process
Among the various anti-corrosion treatment technologies, the phosphating wax dipping process is widely used for protecting drill rods in hydraulic rock drill jumbos. This process is known for its excellent anti-corrosion effectiveness and cost-efficiency.
Degreasing: thoroughly remove the grease and stains on the inner and outer surfaces of the drill rod to lay a good foundation for subsequent anti-corrosion treatment.
Water washing: through multiple water washings, the cleaning agent and stains remaining in the degreasing process are rinsed clean to ensure that the surface of the drill rod is clean and free of impurities.
Surface conditioning: use surface conditioning agents to treat the surface of the drill rod to enhance its surface activity and create favorable conditions for the subsequent phosphating process.
Phosphating: soak in phosphating liquid to form a dense phosphating film on the surface of the drill rod. This film improves the corrosion resistance of the drill rod and enhances the bonding strength with the subsequent coating.
Baking: the phosphate-coated drill rod is heated to dry the surface and reach a specific temperature in preparation for the wax dipping process.
Wax dipping: dip the baked drill rod into the molten wax liquid so that the wax liquid penetrates and adheres to the surface of the phosphating film to form a solid wax layer. This wax layer can further isolate oxygen and moisture in the air and enhance the corrosion resistance of the drill rod.
Advantages of phosphating wax dipping anti-corrosion process
Significantly improve the corrosion resistance: the dual protection of the phosphating film and the wax layer significantly improves the corrosion resistance of the drill rod and effectively extends its service life.
Improve the appearance quality: the surface of the drill rod treated with phosphating wax dipping is smooth, and the color is uniform, which improves the product's overall aesthetics.
Reduce labor intensity: the design of the automated production line reduces manual operations, thus decreasing the labor intensity for workers.
Improve production efficiency: the efficient operation of the production line accelerates the anti-corrosion treatment process for the drill rod, enhancing production efficiency and stability.
Save production costs: optimizing the process and reducing material waste can reduce production costs and enhance the enterprise's competitiveness.
Conclusion
The anti-corrosion treatment of the drill rod for hydraulic rock drill jumbos is the key to ensuring equipment performance and extending service life. The phosphating wax anti-corrosion process has become the first choice of many companies due to its excellent anti-corrosion effect and good economy. With the continuous advancement of technology and constant optimization of processes, it is believed that the anti-corrosion performance of drill rods will be further improved, contributing more to the development of industry and construction.