Join us in advancing geotechnical engineering. Email: una@kellegco.com
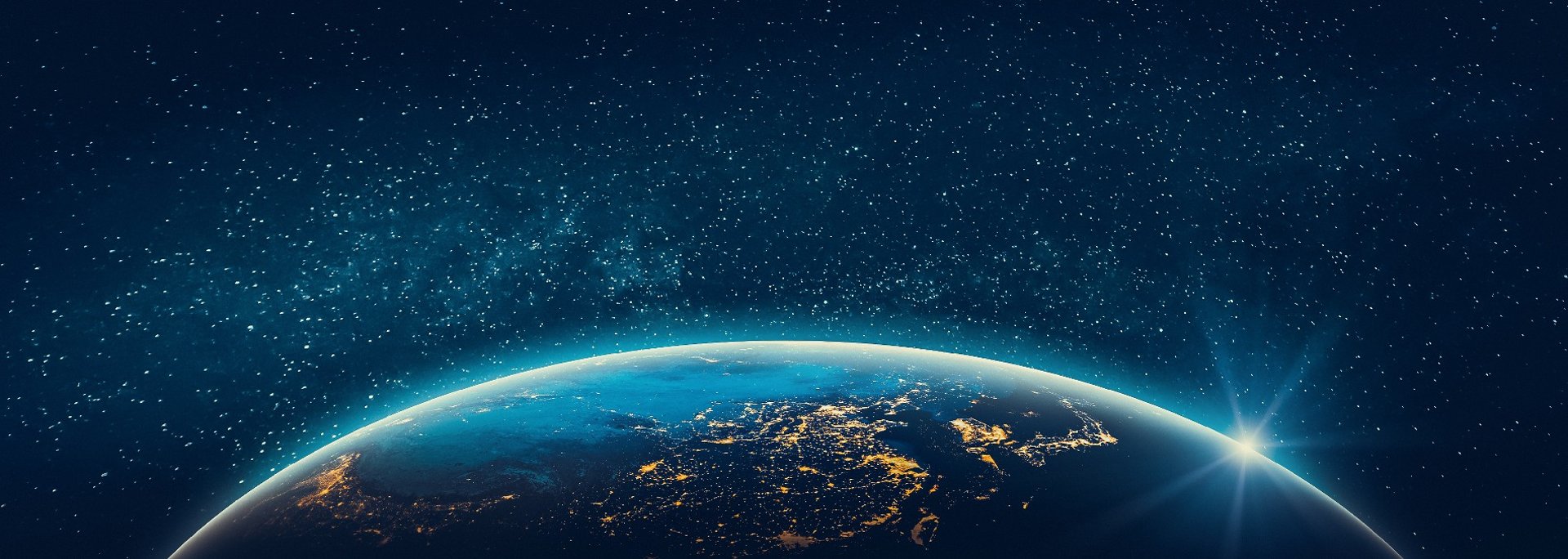
Rock Drilling Tools Definition
Rock drilling tools are special tools used in rock drilling operations to break rocks by impact or rotation.
Una
9/18/2024
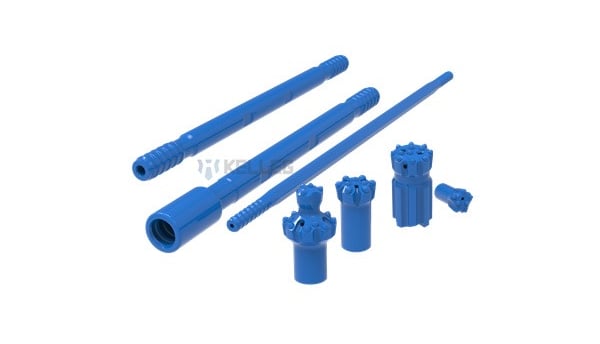
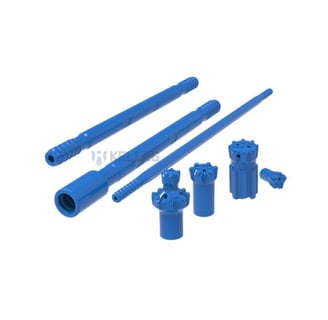
In exploring nature, humans are constantly moving towards unknown areas, and rock, as the hard outer shell of the earth, is both a challenge and an opportunity. Rock drilling tools, seemingly simple but powerful tools, not only unlock the secrets of the rock world but are also a powerful assistant for humans to conquer nature and open up underground space. This article will take you to explore the definition, types, and applications of rock drilling tools and unveil their mysterious and powerful veil.
Definition of rock drilling tools
Rock drilling tools are special tools used in rock drilling operations to break rocks by impact or rotation. It usually consists of a drill bit, a drill rod, a coupler sleeve, and a shank adapter. It is driven by a rock drill or similar equipment to penetrate hard rock layers with high-speed rotation and impact force. Rock drilling tools are necessary tools in mining, tunneling, water conservancy construction, geological exploration, geological disaster management, and other engineering fields.
Types of rock drilling tools
Drill bit
The drill bit is a critical part of the rock drilling tool. Its shape, material, and manufacturing process directly affect the rock drilling efficiency and rock crushing effect. Common drill bit types include chisel bit, cross bit, and button bit, each type has specific application scenarios and advantages.
Drill rod
The drill rod is the bridge connecting the drill bit and the rock drill. It must withstand high-impact force, torque, and bending stress. Therefore, the drill rod is typically constructed from high-strength alloy steel to ensure rigidity and durability. The length and diameter of the drill rod will vary depending on the usage scenario and needs. For example, in tunneling and mining, longer drill rods are often required to meet the needs of deep-hole drilling. In contrast, in some special working conditions, such as underwater drilling or working in high-altitude areas, higher requirements are placed on the corrosion resistance and low-temperature performance of the drill rod.
Coupling sleeve
The coupling sleeve is a threaded sleeve used to connect the drill rod to the shank adapter. It is designed to minimize energy loss during drilling, ensuring that the drill bit receives maximum impact energy.
Shank adapter
The shank adapter is a part connected to the rock drill at one end and to the drill rod at the other end. During rock drilling operations, the shank adapter must withstand high-frequency impact and strong torsion from the rock drill, as well as corrosion and wear from mineral water and slag in the environment.
The role and advantages of rock drilling tools
Improve rock drilling efficiency
Rock drilling tools have significantly improved the speed and quality of engineering construction with their efficient and precise rock drilling capabilities. Through reasonable selection and use of rock drilling tools, we can achieve effective crushing of rocks of varying hardness, thereby accelerating project progress and reducing construction costs.
Enhance operational safety
Rock drilling operations often take place in high-risk environments, such as dust, noise, and vibration. High-quality rock drilling tools can help mitigate these risks and prevent safety accidents caused by equipment failures due to their stability and durability.
Expand application areas
With the continuous advancement of science and technology and the continuous changes in market demand, the application areas of rock drilling tools are also expanding. Rock drilling tools are essential in various fields, from traditional mining and tunneling to emerging underground space development and geological disaster management.
How to choose suitable rock drilling tools?
When choosing rock drilling tools, it is necessary to consider the comprehensive influence of several factors. First, determine the appropriate drill bit type and specifications based on the hardness, properties, and specific requirements of the rock drilling operation. Secondly, pay attention to the performance indicators of the drill rod, such as material, strength, and wear resistance, to ensure that it can withstand the test of various complex working conditions during use. In addition, factors such as the reliability and maintainability of the connecting parts need to be considered to reduce the subsequent maintenance costs and improve the utilization rate of the equipment.
Conclusion
Rock drilling tools are essential for engineering fields like mining, tunneling, and rock crushing. These tools encompass the drill bit that directly contacts the rock, as well as the drill rod and shank adapter that connects the drill bit to the rock drill. They work together to penetrate the rock layer efficiently and accurately, providing the necessary channels for subsequent blasting operations, bolt installation, geological exploration, or direct excavation. With the advancement of science and technology and the continuous upgrading of engineering needs, the material, structure, manufacturing process, and intelligence level of rock drilling tools are also continuously optimized to adapt to more complex geological conditions, improve work efficiency, and reduce labor intensity, thus becoming an indispensable force in promoting modern underground engineering construction.