Join us in advancing geotechnical engineering. Email: una@kellegco.com
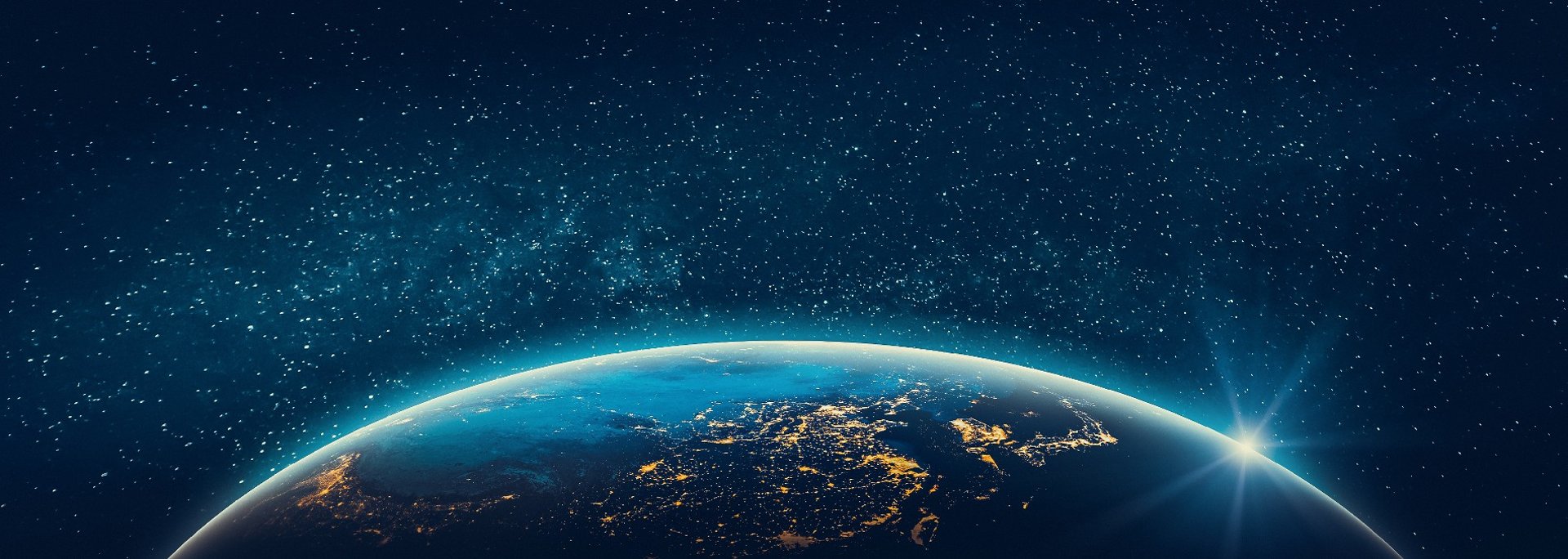
Steel for Rock Drill Bits: High Strength, High Wear Resistance, Improved Drilling Efficiency
As a pivotal tool for converting the impact energy of a hydraulic rock drill into rock-breaking power, the selection of materials and performance optimization of rock drill bits are essential.
Una
9/4/2024
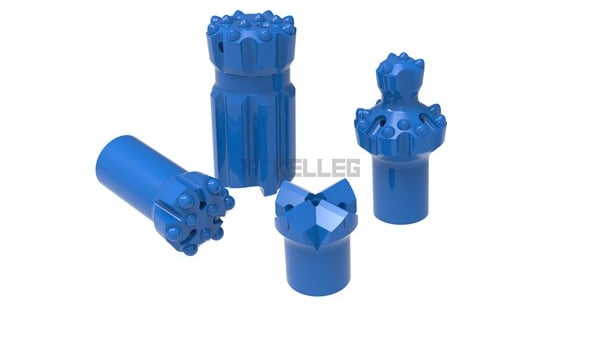
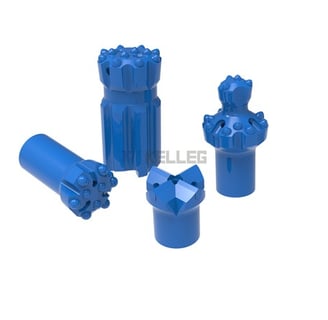
In modern engineering construction, rock drilling is a critical part of foundation construction, and its efficiency and quality are directly related to the progress and cost of the entire project. As a pivotal tool for converting the impact energy of a hydraulic rock drill into rock-breaking power, the selection of materials and performance optimization of rock drill bits are essential. In recent years, advancements in material technology have led to the emergence of a new type of steel for rock drill bits known as HP-2 material. This material boasts high strength, exceptional wear resistance, and excellent anti-tempering stability, making it the preferred choice for enhancing drilling efficiency and reducing construction costs. This article will explore the unique advantages of this new type of steel for rock drill bits.
HP-2 steel for rock drill bits
HP-2 is a new rock drill bit steel made using Si-Mn-Mo microalloying technology. By optimizing the chemical composition and heat treatment process, HP-2 has high strength, high toughness, and excellent anti-tempering stability and exhibits excellent wear and corrosion resistance. These characteristics enable HP-2 materials to exhibit higher wear and corrosion resistance in rock drilling operations, extending the service life of rock drill bits.
High strength and high wear resistance of HP-2
High strength: HP-2 steel has been optimized through careful chemical composition design and a reasonable heat treatment process, thus obtaining extremely high strength. This high strength not only ensures the stability of the rock drill bit during the impact and crushing of rocks but also extends its service life.
High wear resistance: Si, Mn, Mo, and other elements in HP-2 steel work together to form a good wear-resistant structure, effectively resisting rock wear. In addition, HP-2 steel also has a high thermal expansion coefficient, which can better fix the carbide teeth in the hot-setting tooth process, further enhancing wear resistance.
The heat treatment process of HP-2 material
To give full play to the performance advantages of HP-2 material, researchers have conducted in-depth research and optimization of its heat treatment process. The specific steps are as follows:
Quenching stage: heat the HP-2 round steel to 860±10℃ and keep it warm for 1 hour before oil quenching. This process refines the steel grain and optimizes the structure, obtaining higher hardness and strength.
Tempering stage: after tempering treatment at different temperatures (100℃ to 650℃), the material is kept warm for 2 hours and then air-cooled. Through staged tempering, researchers found that HP-2 material can maintain a high hardness (45-50HRC) in the range of 400℃-600℃, thus ensuring the stability of the material in rock drilling operations.
Advantages and applications of HP-2 material
High strength and high toughness: HP-2 material has high strength and good toughness after an optimized heat treatment process. This feature makes the rock drill bit less likely to break when subjected to high-impact loads, improving construction safety.
High wear resistance: using the high hardenability and tempering resistance stability of HP-2 material, the rock drill bit produced can resist rock wear during drilling and extend its service life.
Corrosion resistance: HP-2 material exhibits excellent corrosion resistance, especially in humid or corrosive environments, and it can still maintain good performance stability.
Cost savings: compared with traditional Cr-Ni-Mo materials, HP-2 materials offer similar performance and cost less. Research suggests that using HP-2 materials for rock drill bits can reduce material costs by about 40% and decrease the consumption of scarce resources such as Cr, Ni, Mo, etc.
Conclusion
Applying HP-2 new materials has brought new opportunities and challenges to the rock drill bit industry. By optimizing the material composition and heat treatment process, HP-2 materials have shown excellent performance advantages, providing strong support for improving drilling efficiency and reducing construction costs. We expect this new material to play a more critical role in the wide application in the future and contribute more to infrastructure construction.